Abstract
The Australian Defence Force (ADF) operates in an environment characterised by accelerating and converging change, set against an international context of cooperation, competition and conflict. To meet the Army’s mission of preparing for war, the organisation must undertake a holistic process of modernisation to anticipate the challenges of the future environment. Using available, emerging technology, Army can exploit opportunities to define the operating concepts, structures and personnel required to build a survivable and sustainable force in the future. Through a deliberate, holistic review of supply chains, major platform support contracts and ADF intellectual property ownership, the Australian Army can set the conditions for strategic and operational resilience in our supply chains. In addition, incorporating additive manufacturing technology in a ubiquitous fashion across the entire force will enable resilience of that strategic supply chain. Finally, tactical distribution of these parts, commodities and supplies can take effect in a manner that maximises the capacity of logistics while minimising the threat to soldiers, through the adoption of autonomous and semi-autonomous weapon and vehicle platform technology.
Introduction
For the Australian Defence Force (ADF) to win in the contested, highly lethal battlefields of the future, the force must be both survivable and sustainable. This maxim is particularly applicable to the force’s logistic elements, which are currently structured around operating concepts and doctrine developed during the Vietnam War era, despite the certainty of facing a technologically sophisticated future battlespace of increasing lethality and threat. We offer two proposals for future force concepts and structures. The specific focus of each is on those logistic capabilities that may enable the sustainment of the force in the decades to come, viewed through the lens of the likely future operating environment described in Army’s Accelerated Warfare Futures Statement.
Proposal one describes several options to redefine the supply chains the ADF will be required to rely upon in future conflict. It proposes strategic supply arrangements, capabilities and processes that may increase the resilience of supply chains in a deployed environment. Of particular relevance to ADF operations in a deployed, expeditionary environment, supply chain resilience reduces the likelihood of disruptions to repair parts, combat supplies and commodity supply that may result in a culmination of the force on the battlefield.
Proposal two progresses from the strategic and operational to the tactical: it describes a ground-based distribution model that levers extant and developing semi-autonomous systems. The proposal posits a concept for a more resilient sustainment force that achieves distribution of combat service support to warfighters in highly lethal and contested environments. This maximises the responsiveness and capacity of distribution capabilities, while minimising the exposure of logistic soldiers to unnecessary threat or loss of life. The article concludes with a description of the opportunities currently available to the ADF to start exploring these concepts, to adopt the technology in a limited fashion and to test the structures, operating concepts, techniques and procedures to build an effective, sustainable and survivable ADF for 2030.
Background
Through professional military education activities facilitated by the 1st Combat Service Support Battalion in 2019, the logistic officers of the 1st Brigade held an innovation workshop that considered current autonomous systems and emerging technologies, and sought to predict their relevance and applicability to the future force.1 To demonstrate true military innovation, the workshop set out to define how this technology would impact future force structures, operating concepts and training requirements. The projection for this activity was set at 2030, aligning roughly with existing Army modernisation initiatives such as the 17th Sustainment Brigade vision ‘Logistics 20282 and the ‘Army 2030 Challenge’.3 Using existing research into emerging logistics technology4 to focus the discussions, groups were challenged to create a vision of what they thought the ADF’s future supply chains and ground-based distribution models could look like.
The analysis emerging from this activity, coupled with input from the Defence Science and Technology Group and information incorporated from previous submissions to the Australian Defence Entrepreneurs Forum,7 has led to the development of two complementary proposals. While not representative of views from all logisticians across Defence, the proposals were circulated among the logistic battalions of Army’s combat and sustainment brigades for peer review and input. The final proposals therefore reflect input from a far broader audience than is attributed. The scope of the proposals submitted is constrained to discrete aspects of logistics modernisation: secure strategic, operational and tactical supply chains and ground-based distribution capabilities.
The Future Operating Environment c2030
Accelerated Warfare describes the challenge to Army’s success in future conflict as characterised by four key aspects: geopolitics, threat, technology and domains. The complexity of urbanised and littoral environments in which the ADF is most likely to operate, threat from low-cost swarming technologies and long-range strike capabilities, and vulnerability to attack and disruption in the non-traditional domains of space and cyber all coalesce to present a unique challenge not previously faced by Army.8 This operating environment has two clear implications and challenges for the future sustainment of the deployed force.
Australia’s geography, including its proximity to South-East Asian countries, makes deployed operations in the primary operating environment inherently expeditionary in nature.9 By extension, the ADF is susceptible to significant disruption of both sea and air supply chains with the potential to be cut off during conflict within the region. In addition to geographical constraints, political constraints are conceivable and historical precedents show where a lack of supply chain resilience has impacted Australia’s warfighting capability. The disruption of 84 mm Carl Gustav ammunition supplies during the Vietnam War, due to Swedish opposition to foreign intervention in the conflict, highlights the risk inherent in single-source supply chains and suppliers that reside and operate in foreign countries.10
Within the theatre of operations, the joint land force environment is expected to be a contested, congested, constrained, cluttered and connected battlespace with no definable forward line of troops. Increasingly accurate and lethal munitions exponentially increase the risk of destruction of logistic nodes and assets.11 Complicating this prediction, two-thirds of the world’s population is estimated to be living in the urban environment by 2050.12 Given recent trends in globalisation and urban warfare (Aleppo, Sana’a and Mosul in the Middle East;13 Russian proxy conflict in the Ukraine14) militaries and security forces must prepare themselves for the eventuality that the majority of modern warfare will happen in the urban environment, including megacities.15 Australia’s position in the Indo-Pacific further dictates the high likelihood that deployed operations will occur in the littoral environment, across a number of nations with limited or degraded road infrastructure.16 As such, the distribution platforms our future force operates must be designed to be trafficable across complex terrain: to move with precision through congested streets, utilise smaller turning circles and potentially possess the ability to clear obstacles to their front.
In the context of these two major challenges, two linked proposals follow that represent future force operating concepts that have been developed as standalone yet complementary models of how Army, and the wider ADF, may better prepare the organisation to sustain our forces in the future environment.
Proposal One: Secure Future Supply Chains
Strategic resilience in a deployed environment is, to a large degree, impacted by security of equipment, supplies and parts.17 For an inherently expeditionary defence force, supply chain resilience is a crucial subset of this. The ADF must have ready and responsive access to the parts, supplies and commodities it requires. When this is not achievable, it requires the flexibility to adapt its supply and maintenance systems to maximise force effectiveness.
Historically, Army’s equipment fleets have been subject to restrictive contracts regarding the use of original equipment manufacturer (OEM) specific repair parts and limits to which repairs can be conducted by non-OEM maintainers (specifically, uniformed and Defence contracted members). This has been evident in the constraints of recent support contracts for the heavy vehicle fleet, Harris radios and night-fighting equipment.18 After-sales servicing and spare parts form a highly lucrative portion of these contracts for manufacturers, hence Defence can at times be limited in its ability to use uniformed members to conduct the required work. This significantly impacts ADF ability to maintain this equipment or, in terms of intellectual property (IP) constraints, have military personnel conduct anything more detailed than operator maintenance or light-grade repairs.19 This challenge has the potential to degrade ADF performance in deployed environments, where interrupted access to supply chains and inability to conduct battle damage repair or fabricate substitute parts due to IP restrictions could result in culmination of the force. Security over ADF supply chains thus becomes a substantial concern. Options exist, however, to better manage these concerns.
Foremost among these is a more accurate approach to forecasting inventory requirements. The reduction of inventory and economising of stock holdings at all levels for the first 10 years of the 21st century (to best balance supply chain ‘efficiency’ with mission ‘effectiveness’) was simplistically made possible by calculating prior usage rates as the methodology for estimating expected failures. This antiquated system, however, carried significant risks for abnormal or non-statistically calculated failures (such as battle damage), which resulted in grounding of some assets while awaiting supply chains to fulfil requests for parts. By 2030, edge computing and artificial intelligence (AI) is likely to provide the conduit to provide predictive analysis in real time of the host application. In vehicles and other equipment applications, increases in the number of sensors will facilitate equipment self-awareness and ability to conduct independent built-in tests. Chief of Army Directive 01/19: Land Force Maintenance (CA 01/19) identifies this principle as a key driver of maintenance in our future force.20
As a complement to an improved parts and inventory forecasting system, additive manufacturing (commonly known as 3D printing) as a tool for fabrication and supply is an increasingly attractive option to develop replacement items. Plastics, ceramics, powdered metals and biochemicals/ bio-inks all demonstrate utility for future application; the latter in particular represents a fabrication option beyond traditional spare parts, demonstrating its applicability for organic development in the future.21
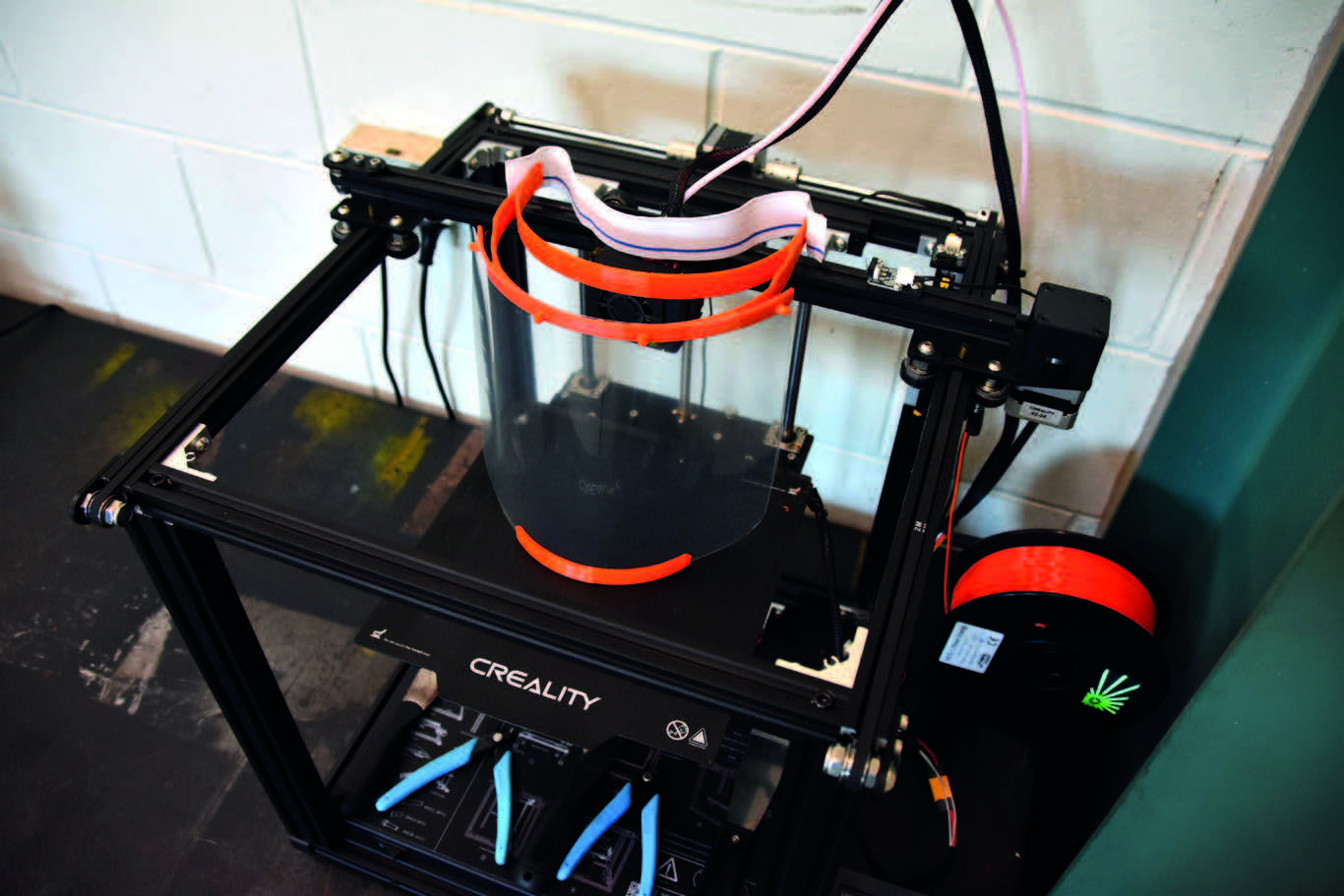
Military application of additive manufacturing is on the rise.22 Capabilities have already been established in the United States military through the US Army’s 299th Battalion Support Brigade, testing a rapid fabrication (R-FAB) capability via additive manufacturing in the Amberg Training Area in Germany in 2018. This expeditionary 20-foot container provides the capability to fabricate multiple types of equipment parts in myriad environments.23 Additionally, the US Navy has successfully constructed a 9.14 m submarine exclusively through additive manufacturing.24 The concept has been explored in academic forums for applicability to military assets with limited resupply ability (such as submarines), utilising 3D printing as a means to enable reliable access to non-safety-critical parts.25 A similar analogy for the joint force could be Army and Air Force elements that are required to operate over expeditionary distances with limited logistic load capacities. The value proposition is simple: it is better to carry raw material capable of being turned into 1,000 different parts than to source and carry 1,000 parts. To date, however, Army has not embraced these opportunities in a holistic way, beyond isolated and limited additive manufacturing procurements in Special Operations Command.
Establishing the Capability
In the first instance, secure supply chains can best be enabled through sovereign capability. Under this proposal, Australian and allied industry ‘ownership’ in 2030 would continue to be promoted within Australia, enhancing long-term sustainability and the upskilling of Australian manufacturing industry, as implemented in the 2017 Naval Shipbuilding Plan.26 The Australian Government’s 10 Sovereign Industrial Capability Priorities (initially established in 2017) have set the groundwork for the establishment of this industry, and in the decades that follow will be expanded upon and matured to capitalise on Australia’s relative wealth of natural resources and rare earth elements (REE: particularly valuable commodities that increasingly figure in sophisticated communications, electronics and alternative energy technologies).27 To align resource security with supply chain resilience, the Australian Government should invest at the national level (or, where financially pragmatic, partner with established commercial entities from partner or coalition nations) in the establishment of high-end processing and manufacturing plants for Defence sub-components that require REE such as lithium batteries, digital communications components, and aircraft assemblies.
Second, the ADF can build strategic resilience through the support contracts developed for major fleet procurements. Future contracts with suppliers and developers should be structured to apply the principles originally established in CA Directive 01/19, to ensure that less-restrictive contracts endorse sovereign production and repair, as well as the required flexibility to meet periods of operational surge. Positive steps have already been taken in this field through recent sovereign production contracts established for the ADF’s next combat reconnaissance vehicle under Project Land 400 Phase Two.28 These contracts would incorporate agreements with potential suppliers to gain early access during development to conduct analysis for mid-development evaluations. Contracts would support functions such as quality control and permit the ADF to identify opportunities for parts commonality between existing and emerging fleets.
Bridging the ‘murky’ area between strategic and operational sustainment, ADF access to parts and supplies can further be secured through supply ‘webs’. To build redundancy, Army should seek to define the ‘full reach’ of where parts are sourced for all major platforms and equipment (supply chain illumination), then diversify suppliers of critical parts and assemblies across multiple locations and providers.29 Suppliers which are located in or aligned with coalition nations would be prioritised for consideration, to build network redundancy in the event of conflict. This would replace traditional ‘single point of failure’ supply chains with supply webs which contain links to where supplies are sourced, where possible including the raw materials for these supplies. Supply contracts through coalition nations lever Australia’s relative REE extraction and processing advantage, by assuring the ADF ‘most favoured nation’ access to critical assemblies produced offshore, in exchange for reciprocal priority access to Australian-produced REE components.30
As the most effective measure under this model, Army would tailor support contracts to ensure IP approvals for the manufacture of repair parts under deployed conditions. Although this authority would be likely to incur a financial premium in contracts, it would afford the simplest guarantee of strategic supply chain resilience when deployed supply networks are impacted. IP ownership could be made possible through contracts structured to provide ‘royalties’ to OEMs each time a part is manufactured in a deployed environment. For high-frequency, low-complexity fabrication in deployed environments, annual licence fees may also be employed for specific fleets as an alternative to the units-based royalties approach.
As highlighted already, IP-enabled additive manufacturing represents a final ‘layer’ of supply chain redundancy to reduce risk in the ADF’s supply chain. In a deployed context, activation of this supply chain can largely be predictive rather than reactive. Using a combination of existing usage rates, augmented with platform-based AI to anticipate conditions-based maintenance and replacement, production of parts would be triggered when the current supply chain is unable to support the required timelines. Where parts that are required for mission-essential equipment are unavailable at a critical point in the battle, automated systems would trigger necessary part production by an R-FAB element in order to provide an intermediate solution.
Staffing and Operating
Future ADF fabrication processes that combine additive manufacturing with traditional trade tools like CNC machines are likely to impact both tactical and operational supply chains.31 Tactical execution of unit-level parts fabrication (by infantry, armour and other combat units) would not occur under this model. Agreed one-time repair limits, driven by the need for battlefield mobility (indicatively two hours), restrict unit tradespeople to perform only expedient battlefield repair by replacing existing parts held by the unit echelon or distributed forward from another node. Arguably, exceptions to this approach exist where forces which are required to operate independently over expeditionary distances may have a smaller, unit-level additive manufacturing capability (indicatively, the amphibious ready element or a regional force surveillance unit).
Tactical execution of formation-level parts fabrication would be achieved through a small production section skilled in additive manufacturing. This organisation would operate from a formation logistic node to support expedient battle-worthiness repairs for mission-essential equipment. The capability would be enabled by three deployable field maintenance modules equipped with additive printing machines to produce expedient plastic, composite and metal parts for non-safety-critical parts (windscreen wipers, windscreens et cetera) or for non-structural battle damage repair (such as metalsmithing of damaged non-ballistic vehicle plating). Part fabrication would be limited in size (currently, 20 cm3 per item) and be suitable for most operating conditions. Each detachment could deploy independently, in order to support multiple dependencies from nodes across a dispersed battlefield—for example, an R-FAB detachment may be attached to a combat service support team supporting a battle group.
Operational execution of force-level parts fabrication would then be achieved through general maintenance support agencies (presently represented by the nascent Close Maintenance Platoon capability held within 17th Sustainment Brigade) taking responsibility for larger projects. In this proposed model, this capability would be constituted as a section. This capability would create high-quality parts and major assemblies which can withstand extreme conditions and either have the required specification or receive certification for use. The size of the 3D printing capability would be comparable to contemporary high-end 3D printers, equivalent to a medium-sized ISO container, albeit with suitably matured technology for 2030.32
To achieve the supply chain redundancy and resilience suggested here, current regulations, policy and doctrine must be permissive enough to allow Army to adapt to rapidly changing technology and situations. Under this model, deployed land force elements must hold the delegation-of-design responsibility to enable greater flexibility under operational conditions and allow for substitution more readily. Unnecessarily centralised authority levels would both increase bureaucracy and undermine the intent of the implementation of a rapid and flexible supply chain. Senior tradespeople or engineers would hold the authority, under a series of standing Engineering Change Proposal approvals, to employ certain vehicle parts as ‘fit for use’.
Through the technical regulatory framework and integrated logistic support instructions for individual platforms and equipment fleets, conditions for the use of additively manufactured parts would be set, defining the duration or operational circumstances in which a specific part can be fitted until an OEM-sourced quality part is acquired. Non-mechanical and non-safety-critical parts and assemblies would be authorised for fitting indefinitely under operational conditions (seats, storage bins and mirrors are likely examples), with formation-level endorsement. Safety critical parts and mechanical assemblies, by contrast, would be fitted for the achievement of a specific mission with a defined period, under the caveats of a ‘battleworthy’ assessment and acceptance of risk by formation commanders. However, to enable responsiveness on the deployed battlefield, this authority could be delegated to unit commanders, with technical endorsement by force-level design acceptance authority representatives.
As a final qualifier on authorities for the employment of this capability, and contingent on the ADF progressively developing this capability over the next 15 years, R-FAB detachments by 2030 would be able to draw from a standardised, Capability Acquisition and Sustainment Group (CASG) endorsed list of many thousands of pre-authorised items which already meet the requisite specifications and requirements for deployed additive manufacturing. Any requirement to print or create an item that does not already exist on this list would simply require approval by the relevant authority through formation and force technical authorities.
Protecting
The operating concepts and structures proposed here are not without risks or challenges. Digitised and networked technology is susceptible to cyber disruption and degradation. The concept of supply chain illumination has illustrated that the industrial controls used to manufacture items or parts, and the supply chain employed to sustain them, are vulnerable to compromise.33 Army can attempt to mitigate this risk for additive manufacturing by operating closed-loop logistics information systems (LOGIS) and employing strategically positioned forward-based stocks of raw materials or, alternatively, holding reserve stocks nationally. Second, the development of compartmentalised and cyber-resistant LOGIS ensures resilience beyond disruption of networks. Finally, the establishment of a global supply chain, leveraging coalition-preferred industries, enables a more resilient supply web for fleets and items for which the ADF cannot obtain IP ownership or deployed fabrication permissions.
Proposal Two: Ground-Based Distribution via Semi- Autonomous Distribution Elements
Whereas this article’s first proposal spans the strategic, operational and tactical levels, the second proposal is intentionally narrow in scope, focusing only on the final link in the supply chain: tactical distribution to the warfighter. For this article, we constrain this further to ground-based distribution within the deployed theatre. The challenges presented to ADF forces by the lethal and contested environment of 2030 demonstrate the case for a force that levers technology to reduce the threat to soldiers. The benefits of autonomous and semi-autonomous distribution systems within the ADF are evident, not for technology’s sake but due to the operational efficiency they afford and the force protection they provide.34
Autonomous systems and vehicle platforms are no longer the stuff of science fiction; as a capability they exist and are subjected to increasing use today. Originally born through military invention35 and developed by civilian companies such as Rio Tinto, Fortescue, Amazon and Google, ‘truck platoons’ are already delivering greater safety and efficiencies across the logistic world.36,37,38,39,40 The concept of a single truck leading up to 10 others, with only one driver and one commander in the lead vehicle, is one that has been developed over the last decade; US and UK forces are already in the later stages of trials for military application.41,42 With the possibility of mid-life-cycle upgrades and vehicle fleet replacements occurring in the next 15 to 20 years, Army’s next generation of distribution capabilities should not only be considerate of but also be specifically designed around the principles of semi-autonomous distribution and ‘truck platooning’.
Operating
The current rear echelon footprint of the deployed Joint Task Force has been superseded by the non-linear battlespace. As posited across a number of public forums and internal Army documents, warfighting in complex littoral and urban environments in 2030 will require support from a greater number of logistic nodes, situated not in a rear-to-front model but rather in ‘inkblot’ footprints that are dispersed across the battlespace.43 Command and control of these nodes will occur in a centralised and network-enabled fashion, to direct and reallocate priorities and main efforts.44 Execution of tasks, however, occurs in a decentralised fashion. Semi-autonomous distribution elements will operate as part of logistic nodes from theatre entry points through to formation and unit areas of operation, delivering to and between combat service support nodes, as well as to unit-level distribution points. No longer will there be a single logistical entry point into a brigade’s area of operations, such as a brigade maintenance area. By contrast, the decentralised approach enables combat service support to be distributed to and from logistic nodes based on a node’s proximity to potential dependency and access to the required classes of supply.
Distribution elements will continually traverse the links between the nodes, with driver/commander crews distributed throughout each location to ensure that as a distribution element arrives at a logistic node it can be rapidly reassigned for subsequent tasking, following short and semi-automated load reconfiguration. Distribution ‘sections’ and ‘troops’ remain the basic functional unit as an administrative structure; however, the internal structure of these organisations has changed (Figure 1). Each distribution troop will retain four sections: two general cargo sections, one heavy cargo section and one specialist section. In a deployed capacity, sections may be task organised, with assets from any or all sections to meet task requirements.
As Army phases out the current LAND 121 (L121) fleet for future deployable fleets (incorporating autonomous driver system functionality as part of initial design), heavy vehicles will move as a manned-unmanned team, in section-sized groups of six vehicles (Figure 1). Midlife upgrades to L121 fleets (40M, 45M and HX77) also make retrofitting of this technology possible for domestic training audiences, enabling force generation through collective training without significant additional financial and engineering impact.
‘Command’ vehicles would be dual-manned by a driver and commander, with the remaining five driverless vehicles ‘slaved’ to the actions of the first. Autonomous programming enables distribution elements to vary speeds, distances and formations for unmanned vehicles in the group, to reduce predictability and pattern-setting. Using a suite of sensors that have been attached during upgrade, command vehicles would record the route, conduct analysis and instantly inform and control the following five vehicles. To ensure redundancy, all vehicles in the platoon would be able to act interchangeably as the command vehicle if required, as well as through a standard human-operated platform. Vehicle manning could be adjusted in environments of differing threat, to provide crew to a second vehicle and provide further redundancy against incapacitation. Manning augmentation would also allow elements to further divide into two capability ‘bricks’ of three vehicles if required to further disperse convoy footprints (Figure 1).
Without established and trafficable road systems, ‘platooned’ distribution elements will only be capable of effecting distribution so far in the urban environment or littoral regions of the ADF’s primary operating environment. Where persistent enemy threat or terrain limitations constrain movement beyond a certain point, unmanned ground vehicles (UGVs) and unmanned aerial systems (UASs) could ensure that the last ‘tactical mile’ of delivery is swift and precise, without exposing soldiers to unnecessary threat. Each vehicle would deploy with two UGVs or UASs as part of the standard complete equipment schedule, or as otherwise task organised. These could be remotely piloted or GPS guided to the appropriate destination. The use of UGVs or UASs for delivery would generally be employed when the conditions are unsuitable for direct distribution. This could span a range of situations, from complex terrain to friendly troops in contact, to a persistent chemical, biological, radiological or nuclear threat that precludes prolonged human presence.
Fighting
While moving through congested, high-threat environments, distribution elements cannot presume to have flanking protection from friendly forces. The commander of the platooned vehicles in this proposed concept would be enabled by an automated front and rear phalanx weapon system on each of the six vehicles in their group, and an intelligence, surveillance and reconnaissance (ISR) feed from teamed UASs that would lead and anticipate their route.
When presented with a threat, the AI-enabled autonomous weapons would present the commander with target options for selection and approval, supported by the on-board battle system that calculates priorities and risk. To address the ethical aspect of autonomous weapon system employment, the task commander remains the ‘human in the loop’ to prosecute pre-selected targets. Once the commander makes a decision, the press of a button would authorise weapon systems throughout the convoy to engage and all networked supporting platforms to respond accordingly.
Supporting and Sustaining
This proposed model would maximise the employment of modularised, ‘smartpacked’ modules that are fitted in varying sizes and weights.45 Load plans for these modules would be calculated by AI-driven LOGIS informed by a networked recognised logistic picture, with the distribution soldier supervising as the ‘human in the loop’. The modules themselves would carry all standard classes of supply, from rations to repair parts. Modularising commodities would enhance the options for how supplies are prepared and configured in a tactically effective manner. Additionally, further modularised capabilities for distribution would include specialised modules for repair, medical support and mortuary affairs; UASs/UGVs linked to semi-autonomous vehicles as CES items, used not only for forward-positioned ISR capability but also to deliver smaller and crucial items through the final most dangerous part of the delivery route; and repair ‘bots’—computerised technician robots that would diagnose and repair vehicle systems.
For a force that has transitioned from legacy diesel-operated heavy vehicles to a highly sophisticated fleet of semi-autonomous systems, current maintenance engineering practices and trades are not structured to support the evolution of technology. In this new paradigm, the majority of maintenance support would be delivered by technicians who are required to support hybrid-powered (or alternative energy) logistic vehicles, ISR sensors, electronic countermeasures and data management systems.
What Can We Put into Practice Now? Opportunities to Prepare the Current Force
These proposals consider a future logistic force that is enabled by technology to adopt different approaches in securing supply chains and distributing to the deployed force. These models cannot be tested or validated without the requisite investment by the ADF now to take practical steps to introduce and build these concepts. What follows are several options available to the ADF to progress these concepts.
Future Supply Chain Opportunities
First, the ADF, specifically through CASG as the delivery group, Army as the capability manager and Joint Logistics Command as the strategic logistic provider, should commence exploration of the feasibility of both strategic and operational supply webs, using multiple means and sources to acquire parts and commodities. This would permit Defence to develop a supply chain ‘PACE’ plan (primary, alternative, contingency, emergency), by commodity, to enable a more dynamic, responsive and resilient logistic network which is maintainable beyond individual option failure. Once developed, strategic and operational PACE plans should be promulgated by Joint Operations Command and joint task forces, within the relevant mission-specific operational orders for scheduled and contingency deployments.
Second, concurrent efforts to develop less restrictive support contracts for major capital acquisitions, espoused under CA Directive 01/19 and underway for a number of impending Defence acquisitions, can be targeted to incorporate clauses endorsing sovereign production and repair, and to enable access by the ADF to IP needed to manufacture parts organically. By developing these contracts over the next 15 years, Army has the opportunity to grow and develop the technical skills of qualified engineers and tradespeople already in Army, within an emerging niche specialisation.
Third, at the formation level and using commercially available technology, Army can introduce additive manufacturing into its support and service organisations now, to trial the concept and employment of the capability. The officers of the 1st Combat Service Support Battalion have begun this journey and are presently working with Army stakeholders to implement such a trial.46 Using a combination of medium and large commercial-sized 3D printers, and targeting repair parts, supplies and commodities for which the ADF holds the intellectual property, this trial will enable the development of tactics, techniques, procedures and governance measures for additive manufacturing as a conventional capability that can be implemented across the wider Army, and the joint force. The potential for expansion to Air Force expeditionary logistic elements and Navy minor and major fleet units is self-evident.
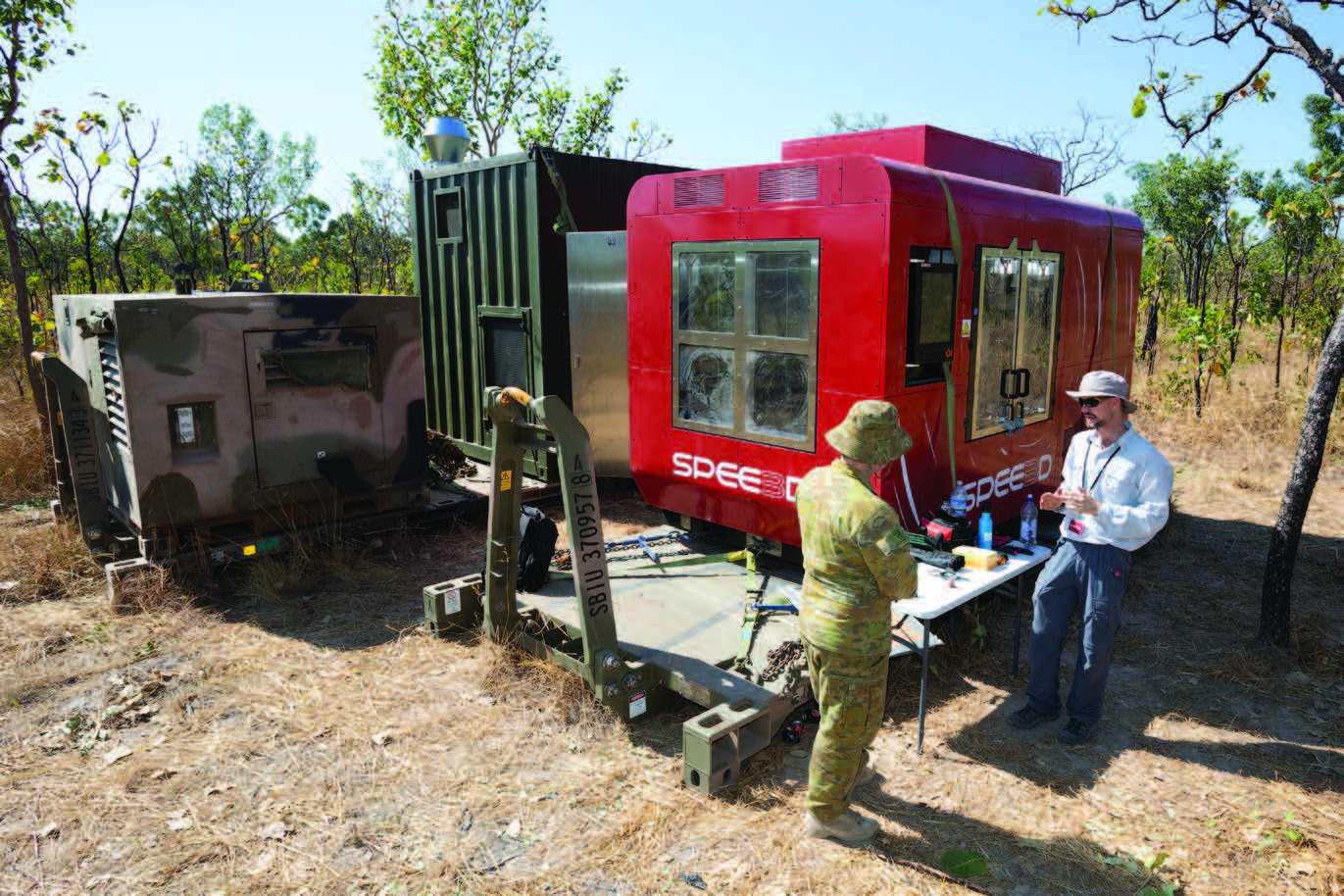
The extension of this trial, once complete, will be the creation of a catalogue of 3D-printable designs for use within Army. This may take a variety of forms but could potentially include an identifiable marker attached to the NATO Stock Number in the ADF’s next enterprise resource program.47 Furthermore, Defence can choose to develop its own 3D-printable designs for subsequent manufacturing, ensuring IP ownership of any designs created as part of the development of this capability. Certain designs may even hold commercial value or be useful for coalition forces. This represents an opportunity to foster genuine military innovation. Future Defence ‘Good Ideas Expositions’ and Army ‘Innovation Days’ could extend the challenge to create 3D printable designs that enhance workplace and job efficiency, prior to codification as part of Defence inventory through the Capability Acquisition and Sustainment Group.
Proposals such as these are not without risk. The quality and quantity of raw materials to conduct additive manufacture must be subject to a control and governance framework ensuring safety and reliability of items manufactured.48 The opportunity to test this concept in order to identify, address and treat the associated weaknesses and risks is too valuable to ignore.
Ground-Based Distribution Opportunities
We acknowledge that the greatest hurdle to overcome in introducing a fleet of semi-autonomous vehicles to the ADF is that the technology is unlikely to be available across vehicle fleets until there is an L121 mid-life-cycle upgrade. Until then, the ADF will focus on what it can achieve in the interim to prepare the force for adoption of this technology.
Disaggregated logistic nodes, centrally controlled and supporting multiple dependencies in a decentralised manner, based on proximity and suitability of supply holdings, represent the first step. This frees support organisations from the traditional echelon structure, thus standardising logistic nodes for ease of planning and allowing for distribution elements to operate as platooned force elements across all nodes. This practice was exercised by task-organised combat service support teams, partnered with combat unit logistic sub-units from the 1st Brigade, through their assignment as Army’s ‘Readying’ brigade during the Joint Warfare Series in 2019. This approach was considered to be widely successful and will be repeated in future iterations.49 The success of this approach is of course predicated on the ability of each node to remain ‘networked’, accessing a recognised logistic picture, generating and receiving demands from across the battlespace and maintaining visibility of force holdings of supply and commodities across the entire theatre of operations. Initiatives within Army’s 17th Sustainment Brigade are currently trialling the development of a recognised logistic picture to make this a reality.50
Greater application of mission command for distribution of force elements in training is another opportunity. This can be achieved by exercising different approaches to the placement of distribution capabilities through an area of operations. Vehicle ownership as a concept could evolve such that vehicles may be transferred between multiple dispersed nodes with different drivers, albeit still ‘owned’ by a single parent organisation. Exploration of command and control structures and platform/equipment handover processes (potentially enabled by onboard vehicle informatic systems that quantify equipment serviceability and CES completeness at the point of handover) would be an essential requirement for, but not necessarily a limitation on, ensuring that this concept is achievable within Army’s governance framework.
Finally, using commercially available products that already exist, the ADF can retrofit semi-autonomous technology to a limited pool of medium and heavy capability vehicles to be capability demonstrators for use in practising the autonomous and semi-autonomous process of distribution through limited trials and ADF major collective training events.
Conclusion
The ADF’s operating environment of 2030 is one that promises challenges and threats in no short supply. It is also one that presents a number of opportunities for the ADF to modernise and adapt its approach to the way the deployed force is sustained in a conflict. Success in this environment is predicated not only on adopting new and emerging technology but also on defining and implementing the operating concepts, force structures and manning requirements that lever and exploit this technology to create a survivable and sustainable competitive edge. The models proposed in this article demonstrate one possible future for how supply chains and distribution are improved in the modern battlespace. Through further debate and analysis on this topic, these models can be considered, challenged and enhanced to shape the ADF of the future.
Endnotes
1 Australian Army, 2019, CO 1 CSSB Directive 03/19: Professional Military Education, 7.
2 Australian Army, 2019, 17th Sustainment Brigade, ‘Logistics 2028: The Vision for the Capability Backbone for Joint Force Sustainment’.
3 ‘Cove Challenge: 2030 Australian Army in 100 Words’, The Cove [website], 6 June 2019, at: https://cove.army.gov.au/article/cove-challenge-the-2030-australian-arm…
4 R Perez-Franco, 2018, ‘What Will Freight and Supply Chains Look Like 20 Years from Now? Experts Ponder the Scenarios’, The Conversation [website], 20 June 2018, http:// theconversation.com/what-will-freight-and-supply-chains-look-like-20-years-from-now-experts-ponder-the-scenarios-98249
5 K Ivanova, GE Gallasch and J Jordans, 2016, Automated and Autonomous Systems for Combat Service Support: Scoping Study and Technology Prioritisation (Defence Science and Technology Group).
6 Defence Science and Technology Group, 2018, Autonomy Based Delivery Systems for Land Logistics: A Study of CSS Force Structure Design Implications, DST-Group-TN-186.
7 J Choi, 2018, ‘LOGBOTS: Swarmed Unmanned Logistic Vehicles’, DEFAUS 2018, Grounded Curiosity [website], at: https://groundedcuriosity.com/wp-content/ uploads/2018/11/181030-DEFAus-18-Article-Dispersed-resupply-logistics.pdf
8 Australian Army, 2019, Accelerated Warfare: Futures Statement for an Army in Motion (Canberra: Commonwealth of Australia).
9 S Kuper, 2019, ‘Supporting the Development of Australia’s Growing Expeditionary Capability’, Defence Connect website, 5 August 2019, at: https://www.defenceconnect. com.au/key-enablers/4526-supporting-the-development-of-australia-s-growing-expeditionary-capability
10 M Henrys, ‘Memoirs of an Armourer’, 5th Battalion The Royal Australian Regiment Association website, at: http://www.5rar.asn.au/narrative/memoirs.htm
11 Australian Army, 2019, Accelerated Warfare: Futures Statement for an Army in Motion.
12 M Konaev, 2019, ‘The Future of Urban Warfare in the Age of Megacities, Focus Stratégique No. 88, at: https://www.ifri.org/en/publications/etudes-de-lifri/focus-strategique/…
13 M Konaev and J Spencer, 2018, ‘The Era of Urban Warfare is Already Here’, Foreign Policy Research Institute website, at: https://www.fpri.org/article/2018/03/the-era-of-urban-warfare-is-alread…
14 B Karabulut and S Oguz, 2018, ‘Proxy War in Ukraine’, The Journal of Defense Sciences 17, no. 1, at: https://dergipark.org.tr/en/download/article-file/477889
15 M Konaev, 2019.
16 McMillan, P, 2019, ‘Ready Now and Future Ready: The Littoral Operating Environment’, Army website, at: https://www.army.gov.au/our-future/blog/amphibious-joint-interagency/ ready-now-and-future-ready-the-littoral-operating
17 G Waters and J Blackburn, 2014, Australian Defence Logistics: The Need to Enable and Equip Logistics Transformation (Kokoda Foundation, Kokoda Paper No. 19), at: https:// www.regionalsecurity.org.au/Resources/Documents/KP19%20LogisticsPaperWe…. pdf
18 Australian Army, 2019, ‘Product Management Plan: Sustainment of CA16 Medium and Heavy Vehicles’ (For Official Use Only); Australian Army, 2019, ‘Product Management Plan: Sustainment of CA29 Surveillance Systems’ (For Official Use Only); Australian Army, 2019, ‘Product Management Plan: Sustainment of CA31 Battlespace Communications Systems’.
19 Ibid.
20 Australian Army, 2019, Chief of Army Directive 01/19: Land Force Maintenance.
21 A Zadpoor and J Malda, 2016, ‘Additive Manufacturing of Biochemicals, Tissues and Organs’, Annals of Biomedical Engineering 45, no. 1: 1–11, at: https://link.springer.com/ article/10.1007/s10439-016-1719-y
22 M Attaran, 2017, ‘The Rise of 3D Printing: The Advantages of Additive Manufacturing Over Traditional Manufacturing’, Business Horizons 60, no. 5: 677–688, at: https://www. sciencedirect.com/science/article/pii/S0007681317300897
23 AB Forces News Collection, 2018, Alamy website, at: https://www.alamy.com/ us-soldiers-assigned-to-bravo-company-299th-battalion-support-brigade-dagger-brigade-test-the-rapid-fabrication-via-additive-manufacturing-on-the-battlefield-r-fab-at-amberg-training-area-amberg-germany-may-4-2018-the-r-fab-is-an-expeditionary-20-foot-container-with-the-capability-to-fabricate-multiple-types-of-equipment-parts-under-multiple-environments-the-testing-is-part-of-joint-warfighting-assessment-jwa-18-which-helps-the-army-assess-emerging-concepts-integrate-new-technologies-and-promote-interoperability-within-the-army-with-other-services-us-allies-and-partners-image184034579.html
24 B Jackson, 2018, ‘Longest 3D Printed Part Guinness Book World Record Set By Made In Space’, 3D Printing Industry website, at: https://3dprintingindustry.com/news/longest-3d-printed-part-guinness-bo…
25 J Kerr, 2019, ‘Underwater Technology: Deep Dive Into Underwater Material Advances’, Australian Defence Magazine 27, no. 8: 38–42.
26 Department of Defence, 2017, Naval Shipbuilding Plan (Canberra: Commonwealth of Australia), at: https://www.defence.gov.au/NavalShipbuilding/Docs/NavalShipbuildingPlan. pdf
27 G Feely and R De Wilde, ‘Supporting a Rare-Earths Industry in Australia’, The Strategist, 12 July 2019, Australian Strategic Policy Institute website, at: https://www.aspistrategist.org. au/supporting-a-rare-earths-industry-in-australia/
28 Department of Defence, LAND 400 Phase 2 Combat Reconnaissance Vehicle (CRVs) (Acquisition) Public Plan, at: https://www.defence.gov.au/spi/Industry/PublicPlans/Public- AIC-Plan-Land-400-Phase-2-Acquisition-Rheinmetall.asp
29 B Mcrea, 2019, ‘Using Multi-Sourcing to Diversify the Supply Chain’, SourceToday website, at: https://www.sourcetoday.com/supply-chain/using-multi-sourcing-diversify…
30 Geoscience Australia, 2013, ‘Applying Geoscience to Australia’s Most Important Challenges: Rare Earths’, at: https://www.ga.gov.au/data-pubs/data-and-publications-search/publicatio…;
31 E Özceylan, C Çetinkaya, N Demirel and O Sabırlıoğlu, 2017, ‘Impacts of Additive Manufacturing on Supply Chain Flow: A Simulation Approach in Healthcare Industry’, Logistics 2, no. 1, at: https://www.researchgate.net/publication/322140889_Impacts_of_ Additive_Manufacturing_on_Supply_Chain_Flow_A_Simulation_Approach_in_Healthcare_ Industry
32 Jackson, 2018. In a commercial context, the world record for the largest solid 3D-printed item is currently held by Oak Ridge National Laboratory for producing a printed ‘wing trim tool’ in 30 hours, with a weight of 726 kg (printed in a combination of carbon fibre and plastic). As a planning tool, on average, it takes five hours for a 3D printer to print its internal dimensions in plastic (the larger the machine, the larger the dimension that can be printed in five hours); this time can be reduced if the quality of the fabrication is reduced. The current price of the largest industrial 3D printer (Objet1000 Plus, Stratasys) is approximately US$250,000, with a maximum printing size of 1000 mm x 800 mm x 500 mm, which is capable of fitting on an in-service flatrack.
33 L Wainstein, ‘7 Supply Chain Security Concerns to Address in 2019’, The Network Effect: Beyond Supply Chains [website], 10 December 2018, at: https://supplychainbeyond. com/7-supply-chain-security-concerns-to-address-in-2019/. Methods of LogIS compromise may include, but are not limited to, traditional security threats such as cyber attack to disrupt or degrade communications, or infiltration and manipulation of LogIS to disrupt and redirect the flow of items through the supply chain.
34 M Murison, 2018, ‘Pentagon: Military Will Have Self-Driving Vehicles before Public, Internet of Business website, at: https://internetofbusiness.com/pentagon-military-self-driving-vehicles/
35 Defense Advanced Research Projects Agency (DARPA), 2015, ‘The Grand Challenge’, DARPA website, at: https://www.darpa.mil/about-us/timeline/-grand-challenge-for-autonomous…
36 Rio Tinto, 2016, ‘Driving Productivity in Pilbara: Trucks Driving Themselves Around the Red Dirt Landscape’.
37 G Nott, ‘Fortescue to Establish Autonomous Vehicle R&D Hub’, CIO website, 26 March 2019, at: https://www.cio.com.au/article/659266/fortescue-establish-autonomous-ve…
38 O Mitchell, ‘Amazon Keeps on Truckin’ With Autonomous Vehicle Investments’, The Robot Report [website], 25 February 2019, at: https://www.therobotreport.com/amazon-autonomous-vehicle-invest/
39 B Marr, ‘Key Milestones of Waymo: Google’s Self Driving Cars’, Forbes [website], 21 September 2018, at: https://www.forbes.com/sites/bernardmarr/2018/09/21/key-milestones-of-w…
40 M Milford, ‘Coming Soon to a Highway Near You: Truck Platooning’, The Conversation [website], 20 November 2017, at: https://theconversation.com/coming-soon-to-a-highway-near-you-truck-pla…
41 A Hittle, A, ‘US Army Awards Oshkosh Defence $49 Million to Bring Autonomous Technology to the Battlefield’, Oshkosh Defense website, 27 June 2018, at: https:// oshkoshdefense.com/u-s-army-awards-oshkosh-defense-49-million-to-bring-autonomous-technology-to-the-battlefield/ 100
42 G Evans, 2018, ‘Driverless Vehicles in the Military: Will the Potential be Realised?’, Army Technology website, 12 February 2018, https://www.army-technology.com/features/ driverless-vehicles-military/
43 M Baldock, 2017, ‘Survive First, Sustain Later: Exercising Dispersed Logistics in the Close Fight’, Logistics in War website, at: https://logisticsinwar.com/2017/03/14/survive-first-sustain-later-exerc…; Australian Army, 2019, Brief to CA (through COMD FORCOMD) on the Operational Sustainment Mission Analysis of Accelerated Warfare (For Official Use Only).
44 The Cove, 2019.
45 Australian National Audit Office (ANAO), 2015, Australian Defence Force’s Medium and Heavy Vehicle Fleet Replacement (Land 121 Phase 3B), ANAO Report No. 52, 2014–15, Performance Audit (Canberra: Commonwealth of Australia), at: https://www.anao.gov. au/work/performance-audit/australian-defence-forces-medium-and-heavy-vehicle-fleet-replacement-land-121
46 Defence Entrepreneurs Forum Australia (@DEF_Aus), ‘… we will see 3D printing in 1 Bde next year’, @DEF_Aus Twitter post, 1 October 2019.
47 R Pearce, ‘Defence Prepares for Massive ERP Overhaul’, Computerworld [website], 23 May 2016, at: https://www.computerworld.com.au/article/600281/defence-seeks-system-in…
48 I Wing, R Gorham and B Sniderman, ‘3D Opportunity for Quality Assurance and Parts Qualification: Additive Manufacturing Clears the Bar’, Deloitte Insights, 18 November 2015, Deloitte website, at: https://www2.deloitte.com/us/en/insights/focus/3d-opportunity/3d-printi…
49 LTCOL T Stone, ‘Exercise TALISMAN SABRE Performance Report: Senior Observer Trainer—Brigade Support Group’ (For Official Use Only), 25 July.
50 Australian Army, 2019, ‘17 Bde: Joint Warfighting Series 2019—Trial, Test and Evaluation Structure’ (For Official Use Only), 26 April.